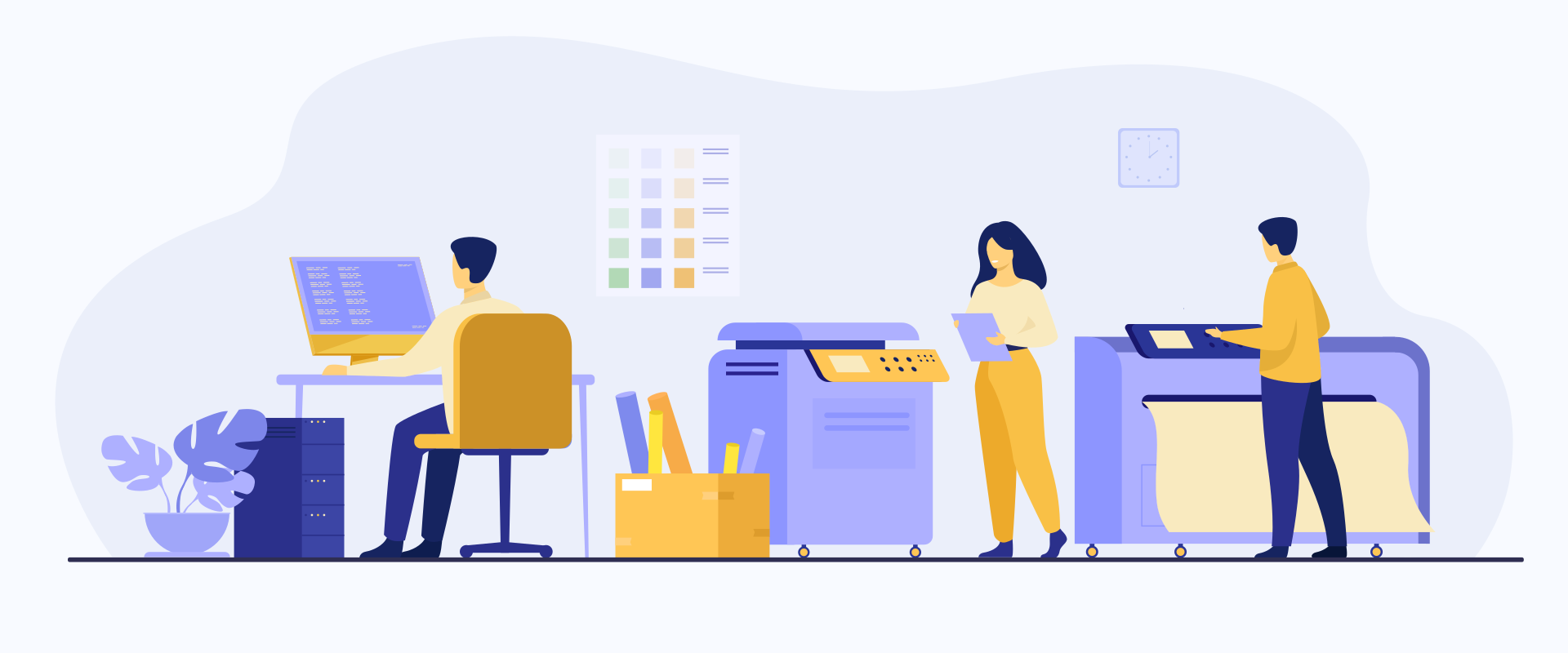
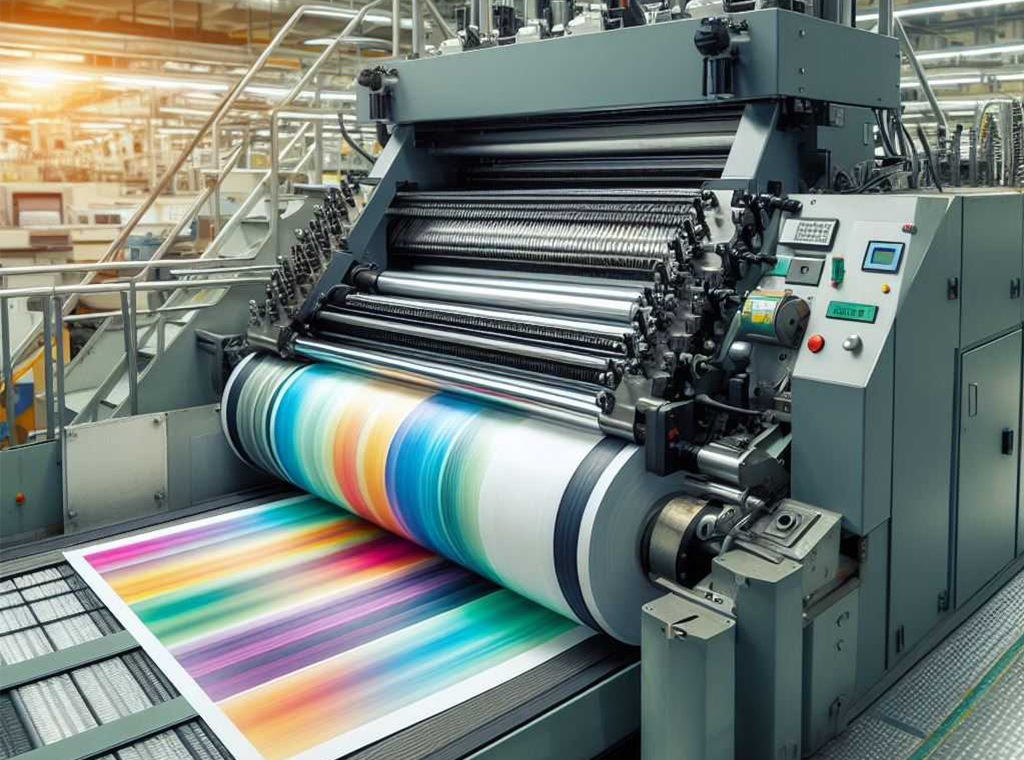
Kattrapin Technologies
With more than 20 years of experience in the printing business, we are the go-to company for high-quality, exceptional printed materials. We deliver the very best in print quality with outstanding service at competitive rates. With a commitment to customer satisfaction, we consistently strive to exceed our clients’ expectations.
Why us?
High-quality printing
We ensure your business looks its best with top-quality print jobs, done right and delivered on time. With us, you get exceptional value and outstanding quality.
Best price
We take pride in offering superior-quality printing at the best possible price. When you work with us, you can be confident you are getting the best value for your money.
Fast turnaround
Since we understand that your time and financial resources are extremely important, we help you meet your deadlines with our fast turnaround.
Our services
Our combination of high-quality, cost-effective, and on-time delivery ensures operational excellence. From business cards and brochures to catalogs and promotional materials, we deliver exactly what you need—right on time.
Our facilities
Experience flawless printing with our state-of-the-art commercial facilities, operated by skilled professionals.
Our products
o We continuously invest in and refine our products to ensure the highest quality. Our unbeatable combination of price and excellence keeps customers coming back!
Our Clients
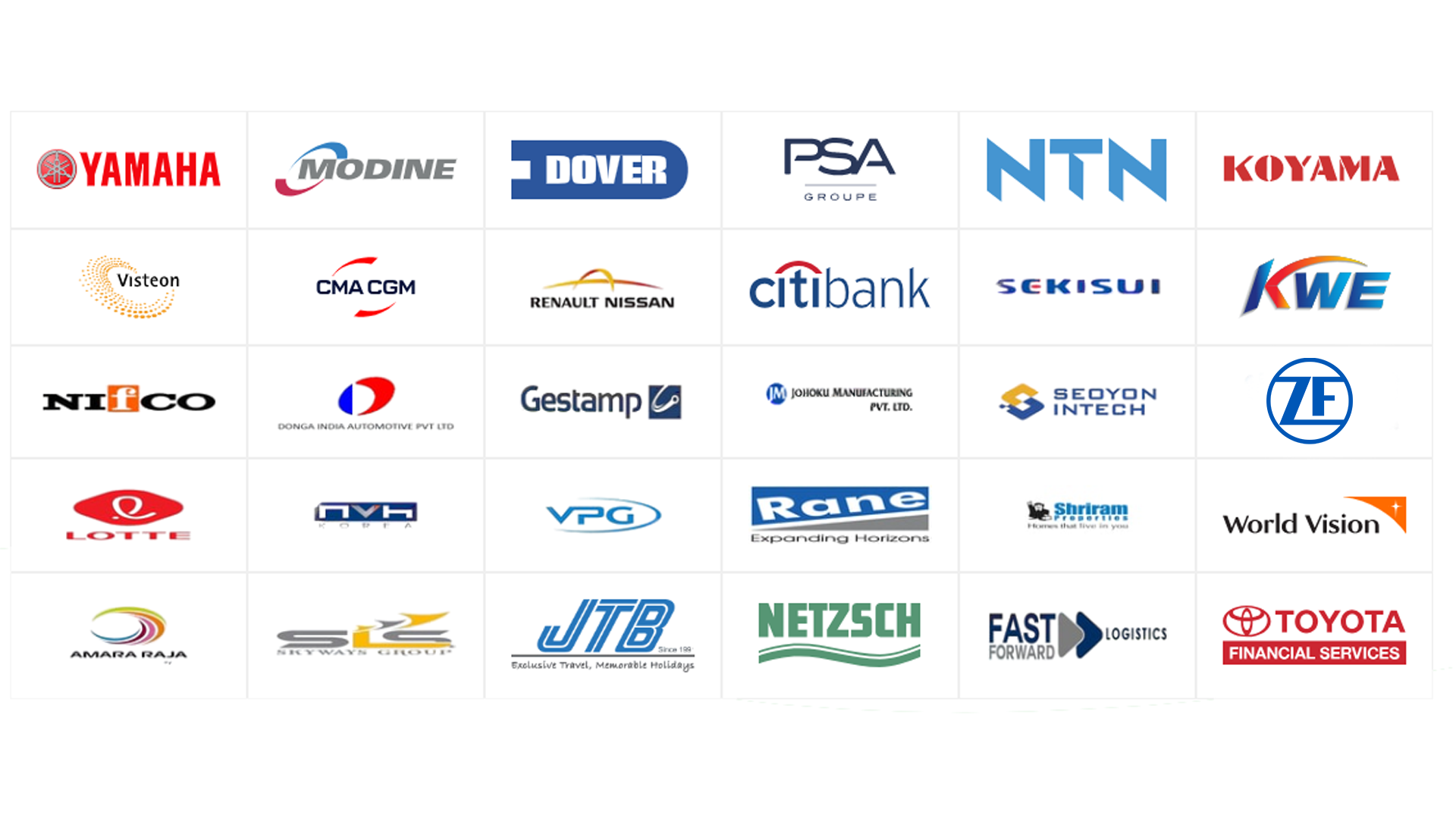
We create detailed user manuals and owner’s guides that help end users understand how to operate, maintain, and troubleshoot their vehicles. Our documentation is written in clear, easy-to-understand language, with step-by-step instructions and visual aids to make vehicle handling and upkeep simple.